Common Pipeline Anomalies Detection Mistakes in Corrosion Management
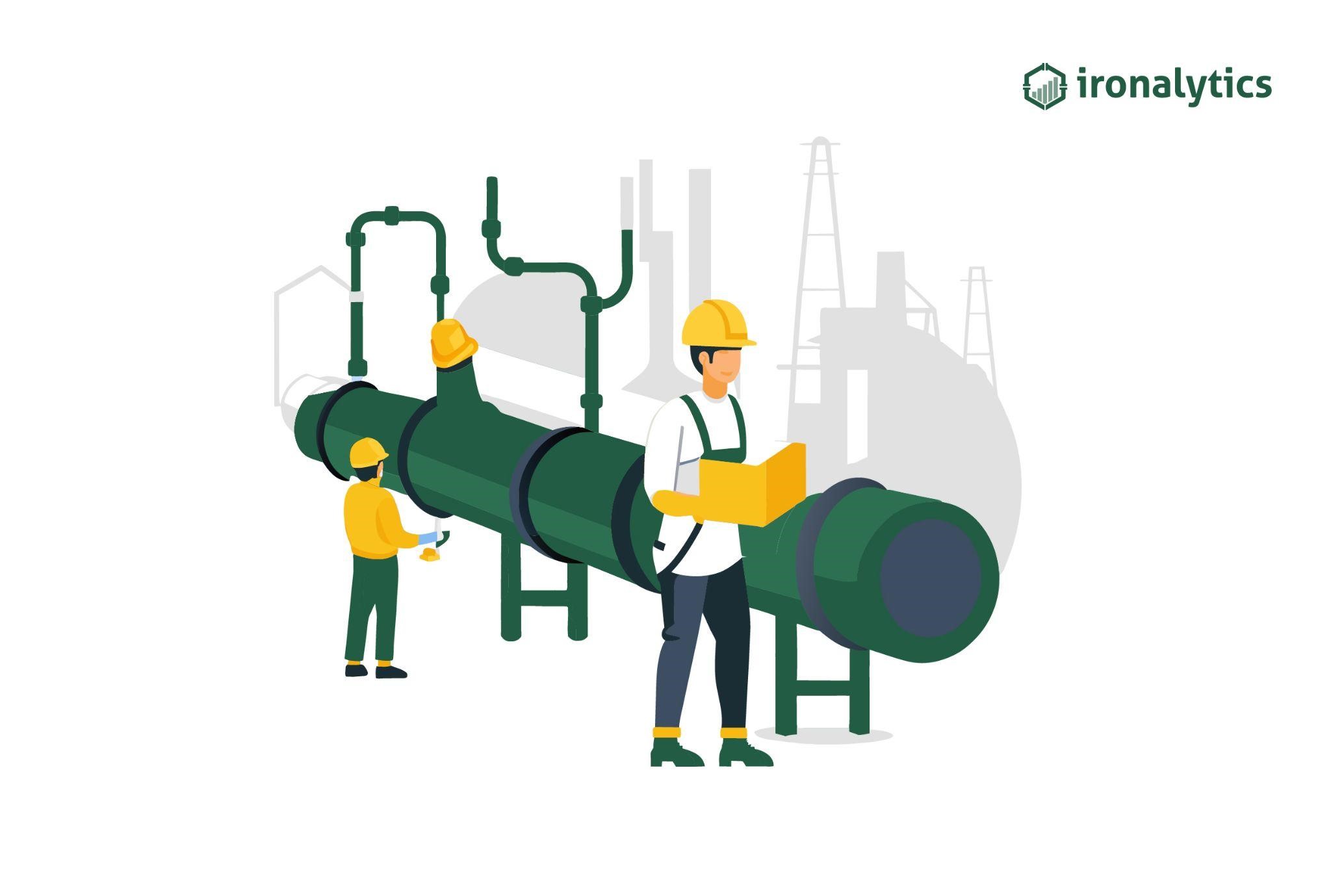
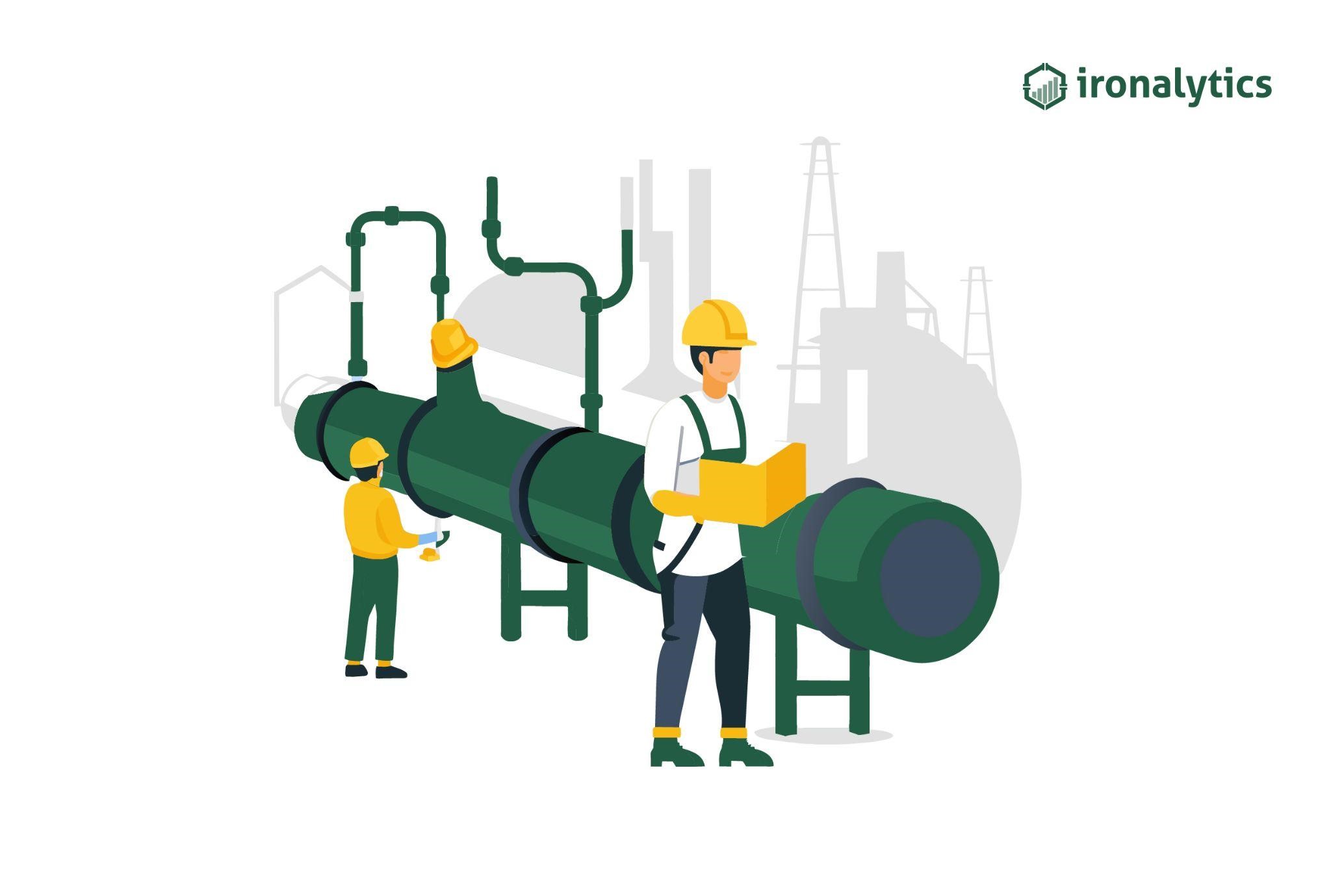
Effective pipeline integrity management ensures long-term operational efficiency and prevents costly failures. However, Pipeline anomaly detection mistakes can accelerate deterioration and increase Pipeline Integrity risks. When overlooked, such mistakes can undermine the integrity of the pipeline, leading to expensive repairs, safety hazards, and environmental damage. To safeguard against these pitfalls, it's crucial to be aware of common pipeline anomaly detection mistakes, including inadequate initial assessments, improper material selection, neglecting coating maintenance, and poor monitoring.
Common Mistakes in Pipeline Anomaly Detection
Given below are the common Pipeline anomaly detection mistakes that usually occur due to a lack of regular monitoring and human errors:
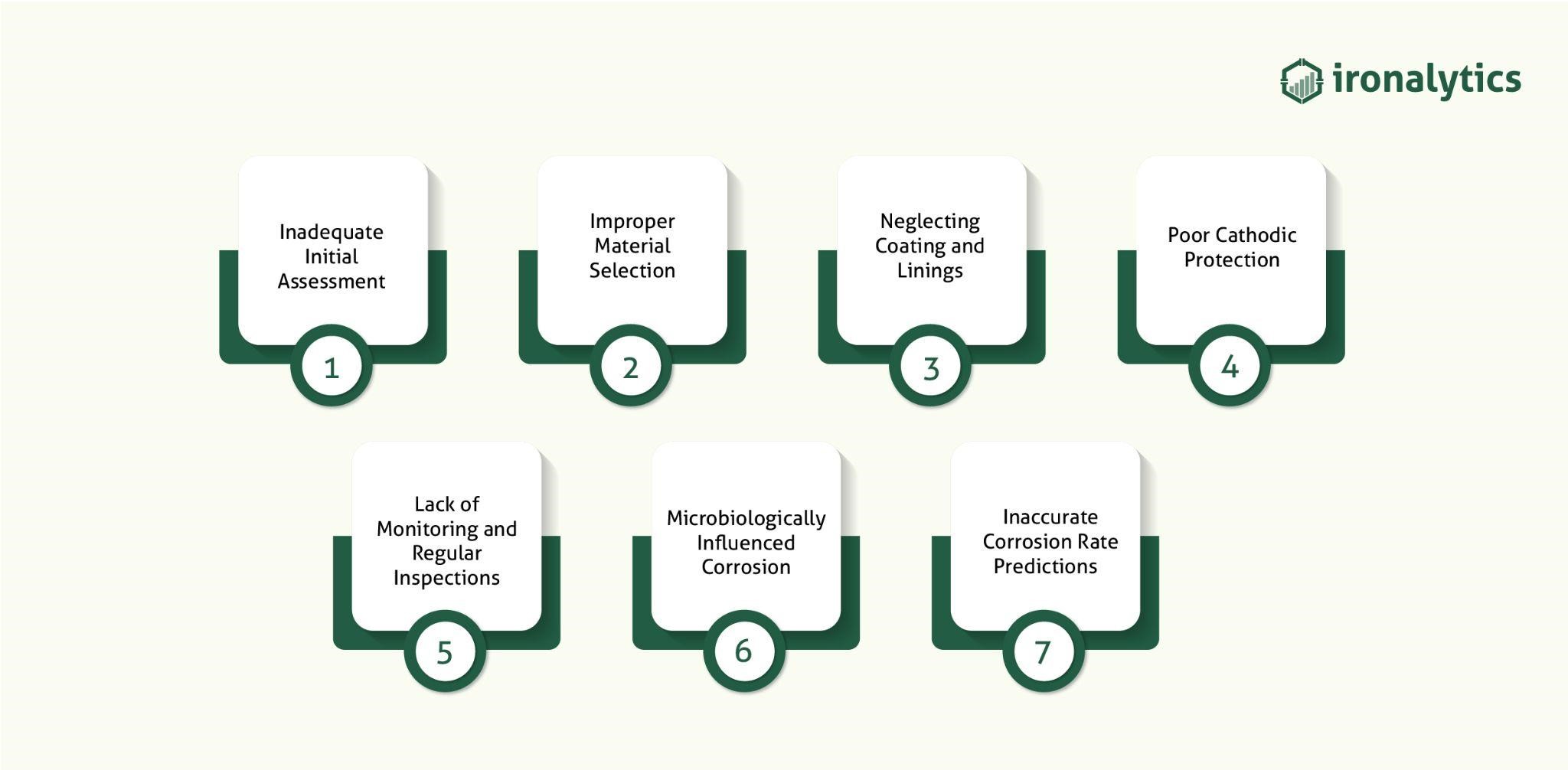
1. Inadequate Initial Assessment 2. Improper Material Selection 3. Neglecting Coating and Linings 4. Poor Cathodic Protection 5. Lack of Monitoring and Regular Inspections 6. Microbiologically Influenced Corrosion 7. Inaccurate Corrosion Rate Predictions
Inadequate Initial Assessment
One common Pipeline anomaly detection mistake in pipeline management is skipping a full assessment of the pipeline's environment, material, and history. This step is crucial because it helps identify key factors like soil type, humidity, external pressures, and how the pipeline materials have held up over time. Without this information, it’s hard to create effective corrosion management plans. Consequences: ● Inability to detect potential environmental hazards that could accelerate corrosion. ● Implementation of unsuitable corrosion management practices. ● Increased risk of pipeline leaks, failures, and costly repairs. ● The shortened lifespan of the pipeline is due to unaddressed environmental factors. ● Inefficient use of resources in managing pipeline integrity. Conducting thorough environmental studies and risk assessments before applying corrosion management strategies is critical to avoid such issues. This involves a comprehensive analysis of soil composition, humidity levels, and the operational environment the pipeline will endure. By understanding these factors, you can tailor corrosion management practices to the specific conditions, reducing risks and ensuring the pipeline’s durability.
Improper Material Selection
Choosing materials that don’t match the pipeline's specific environment is a common mistake in pipeline management. In various situations like saltwater exposure, high temperatures, or acidic soils, can react negatively with certain materials. For example, in a high saltwater environment, it will corrode faster if carbon steel pipelines are used in such environments, causing the pipeline to wear faster. Consequences: ● Fast material deterioration and quicker onset of corrosion. ● Increased maintenance costs and frequent repairs. ● Higher likelihood of pipeline leaks or failures. ● Shortened pipeline lifespan due to material incompatibility. ● Potential safety hazards from unexpected pipeline breaches. In such conditions, pipeline operators should opt for corrosion-resistant materials like stainless steel or coated pipes, they can greatly extend the lifespan of the pipeline. Selecting the appropriate materials from the start helps avoid potential issues down the line and ensures the pipeline operates efficiently for many years.
Neglecting Coating and Linings Maintenance
Skipping regular maintenance of protective coatings and linings is a big mistake in pipeline management. These coatings act as the first line of defence against moisture, chemicals, and wear. Over time, they can break down due to tough conditions or poor application. If they're not properly maintained, they stop protecting against corrosion, making the pipeline more vulnerable to damage. Consequences: ● The pipeline's exposure to corrosive elements results in faster corrosion. ● Increased likelihood of leaks, pipeline breaches, or system failures. ● Expensive repairs or replacements due to severe damage. ● Lifespan Reduction of pipeline and overall operational inefficiency. ● Increased safety risks, particularly in essential infrastructure such as oil and gas pipelines. Pipeline operators should constantly monitor for signs of wear, cracks, or peeling and repair damaged areas promptly to avoid such risks. Also, they should use high-quality, corrosion-resistant coatings suited to the specific environment, which can significantly enhance protection.
Poor Cathodic Protection
Cathodic protection (CP) is a crucial method used to prevent corrosion on metal surfaces, such as pipelines, by controlling the electrochemical reaction that causes corrosion. However, improper design, installation, or maintenance of a cathodic protection system can severely compromise its effectiveness. This often occurs due to incorrect CP system sizing, poor monitoring, or insufficient current flow to the pipeline. As a result, the pipeline remains vulnerable to corrosion despite the CP system being in place. Consequences: ● Inadequate protection of the pipeline, leading to continued or accelerated corrosion. ● Ineffective use of resources and increased maintenance costs. ● Potential pipeline leaks, ruptures, and environmental hazards. ● Regulatory and Legal issues like fines and legal action. To avoid such common pipeline anomaly detection mistakes, the pipeline operator or company should calculate the amount of current needed to protect the pipeline based on its size, length, and environmental conditions. Also they should hire experienced corrosion control experts who can also help in customising the CP system to fit the pipeline’s specific needs.
Lack of Monitoring and Regular Inspections
Some Pipeline anomaly detection mistakes happen because of poor monitoring and irregular inspections. Pipelines are always exposed to various environmental and operational conditions that can accelerate corrosion or cause other types of damage. Without regular inspections and real-time monitoring, issues such as coating degradation, cathodic protection failure, or unnoticed corrosion can go undetected until they cause severe damage. Consequences: ● Early signs of corrosion or damage go unnoticed, leading to accelerated pipeline deterioration. ● Higher repair costs due to the late detection of problems. ● Reduction in overall pipeline operational efficiency. ● Risk of environmental contamination and regulatory non-compliance. The key to preventing these issues is implementing a robust monitoring and inspection schedule. This includes various operations like: - Regular visual inspections - Advanced non-destructive testing (NDT) methods - Real-time monitoring systems These allow pipeline operators to track the pipeline’s integrity and environmental conditions to avoid any risks.
Microbiologically Influenced Corrosion (MIC)
When pipelines are exposed to certain environmental conditions where they get affected by certain types of bacteria or microbes. They accelerate the corrosion process on pipelines. These microorganisms can thrive in environments like water, soil, or within the pipeline itself, producing by-products that contribute to corrosion. Overlooking the presence of MIC in corrosion management is a critical mistake, as it can render standard prevention methods ineffective. MIC often occurs in pipelines carrying water or chemicals, where bacteria can form biofilms that intensify corrosion. Consequences: ● MIC accelerates the corrosion process, causing faster deterioration of the pipeline. ● Standard corrosion prevention methods may fail, leaving the pipeline vulnerable. ● Increased repair and maintenance costs due to rapid pipeline degradation. ● Higher risk of leaks, environmental contamination, and safety hazards. ● Potential for unplanned operational downtime and significant financial losses. To address microbiologically influenced corrosion (MIC), it’s important to integrate specific prevention methods. Key prevention methods include: - Regular Microbial Assessments - Biocide Treatments - Specialised Coatings - Pipeline Design Considerations
Inaccurate Corrosion Rate Predictions
Among other common Pipeline anomaly detection mistakes, pipeline operators relying on outdated or inaccurate corrosion rate predictions are very common due to either manual reading or human error. Corrosion rates can be different based on different environmental changes, operational conditions, and material degradation over time. And using outdated models fail to account for real-time changes, they may underestimate or overestimate how quickly corrosion occurs. This can result in poor planning for maintenance, causing either unnecessary costs or, worse, pipeline failure. Consequences: ● Mistimed maintenance schedules, either too early or too late. ● Increased risk of pipeline leaks, ruptures, or catastrophic failures due to undetected corrosion. ● Higher operational costs from unexpected downtime or emergency repairs. ● Reduced pipeline lifespan due to inadequate protection measures. ● Safety hazards and potential environmental damage from unforeseen pipeline failures. So, pipeline companies must use advanced tools to monitor and gather pipeline data. The advanced tools and methods to prevent getting wrong corrosion rates are given below: - Updated Corrosion Prediction Models - Real-Time Monitoring Sensors - Advanced-Data Analytics Platforms - Predictive Maintenance Systems - Regularly Updated Corrosion Prediction Models These tools enable predictive maintenance, ensuring that pipeline inspections and repairs occur at the right time, preventing premature failures and optimising the pipeline’s longevity and performance. Regularly updating corrosion prediction models based on recent data also helps in making informed decisions for long-term pipeline management. Well following preventive and advanced technologies will help you to avoid these common pipeline mistakes. However using an extra help of Pipeline integrity management software will not only reduce multiple preventive maintenance but also increases the overall efficiency of pipeline integrity management. And one such software is Ironalytics.
Our Solution to assess Pipeline Corrosion & predict remaining life- Ironalytics
Ironalytics is a comprehensive platform built to streamline pipeline integrity management for industries dealing with complex data and operational challenges. Its primary focus is on enhancing safety and efficiency by automating data integration and threat analysis, covering critical areas such as cracks, dents, corrosion, cathodic protection, and right-of-way (ROW) concerns. Key Features of Ironalytics: 1. Pipeline Integrity Digitalisation: Ironalytics centralises data from various sources, providing clear, actionable insights into pipeline health. With customisable dashboards, geotagging capabilities, and automated integrity KPIs, monitoring and reporting are simplified and accessible on any device. 2. ROW/Integrity Management: The platform monitors right-of-way (ROW) events, such as encroachments or third-party activities, ensuring legal compliance and minimising downtime. Integrated with drone surveillance, Ironalytics offers real-time tracking and alerts for more efficient management. 3. Defect Assessments and ILI Analysis: Ironalytics automates in-line inspection (ILI) assessments, offering detailed visualisations based on industry standards. It predicts corrosion, metal loss, and the remaining lifespan of pipelines, allowing for proactive maintenance planning. 4. Geospatial Analysis: Utilising Google Maps, the platform delivers geospatial visualisations of pipelines, displaying asset locations, risk zones, and historical anomalies, empowering informed decision-making. 5. Risk Management: Ironalytics automates threat detection and builds risk profiles in compliance with ASME and API standards. This enables operators to identify high-risk areas and take preventative actions. 6. SCADA Integration: The platform integrates with SCADA systems, allowing for real-time analysis of product quality and internal corrosion modelling. This helps predict maintenance needs and prolongs the lifespan of pipelines.
Conclusion
Managing pipeline integrity effectively requires a proactive and well-rounded approach to avoid common pipeline mistakes that can lead to costly repairs, environmental damage, and operational inefficiencies. Incorporating a PIMS like Ironalytics further simplifies the process by centralising data, automating threat detection, and integrating geospatial analysis and SCADA systems for enhanced pipeline management. Book a demo today to explore how Ironalytics can safeguard your pipeline infrastructure.